01
数字化车间的自动化设备联网与数据采集实践
一、前言
航空制造作为高端离散制造业的典型代表,为了对制造现场的资源完成集约束管理,需要对企业经营业务实现数字化管理,从而带动资源要素的价值链升级数据采集。首先,在生产生命周期中,主要通过对设备联网集成技术、制造过程在线监测技术、工业大数据技术等关键技术的应用,构建以 MES 系统为核心驱动的数字化、网络化的企业集成应用业务平台;其次,在产品生命周期中,主要从产品需求收集、设计工艺协同、生产制造、售后运维、产品报废的各个阶段,通过对SCM、PDM等系统的深度融合集成,全面实现高端装备产品从设计、加工、装配、检测、质控,
到物流、服务全数字化贯通数据采集。
本文主要从生产生命周期角度出发,针对数字化车间的构建过程,阐述实现智能制造涉及的设备数据采集技术以及互联互通技术的实践与应用数据采集。
二、数字化车间架构
数字化车间以生产对象所要求的工艺与设备为基础,通过将制造技术与信息化、网络化、自动化以及现代管理理念相结合,借助数据连接车间不同单元,从而在车间形成数字化制造平台,对车间生产运行过程中的管理和生产等各环节进行规划、管理与优化,从而支持智能制造数据采集。数字化车间的核心是MES为主体的数字制造执行系统,它以SCADA系统采集到的现场实时数据为源头,借助自动化和智能化的技术手段,实现车间制造控制智能化、生产过程透明化、制造装备数控化和生产信息集成化的目标。数字化车间的总体架构如图1所示。
图1 数字化车间架构
C#通过OPC UA+MQTT将设备数据采集至云端-自动化工程师的数字化之路
最全整理工业通讯上的领域各种总线+协议+规范+接口—数据采集与控制
MES、SCADA项目中的数据采集—基于C#与研华IO模块的ModbusTCP通讯
生产过程中实时准确地制造信息能够帮助管理者了解设备加工情况以及综合利用率,同时还可以满足对生产过程管控和质量管控的需求,从而掌握企业的生产节拍,并根据数据辅助企业管理者进行智能决策[9]数据采集。车间制造过程数据总体上可以分为三大类,分别是 : 静态数据、动态数据以及中间数据,具体含义如下:
1.静态数据通常指不会发生变化的数据,是企业的静态参数信息,用于帮助了解企业的生产资源、生产经营能力等信息数据采集。静态数据如物料的编码、加工者的内部编号、加工设备编号、库房编号等。
2.动态数据通常指变动的信息数据,是在制造生产过程中随着零件状态的变化而发生变化的一类数据,主要来源于生产部门在各时间点产生的生产经营相关的数据信息数据采集。动态数据包括零件的加工工序、尺寸、物流信息、开工完工时间、零件状态等。
3. 中间数据通常是从管理者的角度出发,对采集的静态数据与动态数据进行有效地整合与处理,由此而产生的数据就是中间数据数据采集。例如,管理系统有时需要对数据进行批量处理,对数据进行格式化,以满足处理或模块之间的通信需要。
三、设备数据采集系统方案设计
(一)系统需求分析
数据采集系统通过对车间生产数据进行采集、检测、统计与分析,实现对制造现场的有效管理,支持企业管理层与现场自动化控制设备之间的信息互通数据采集。
考虑到制造现场设备种类繁多、设备间实时性传输且各种数据库系统异构情况突出等实际状况,工业大数据具有并发数大、异构性强、关联性强、状态复杂多变等特征,并且需要持续采集,具有鲜明的动态时空特性数据采集。因此,如何对现场生产数据进行采集、存储、管理、建模、交换、分析和使用,已经成为当前军工制造企业普遍存在的难点和亟需解决的问题。
主要体现在以下几个方面:
1. 车间分期建设数据采集,规划不统一,多源、异构数据信息采集困难,设备接口复杂多样,生产中存在信息孤岛;
2. 设备无法依据计划、工艺要求、参数配置自动加载、切换程序数据采集,同信息化系统中间有断层;信息化系统结构化、半结构化和非结构化数据多而复杂,数据压缩、存储、交互困难;
3. 产品设计过程中未考虑信息交换数据采集,导致制程跟踪信息丢失;工艺设计过程中未考虑信息交换,造成生产系统缺乏监测管控手段;存在大量的手工录入环节,错误率高,时效性差;
4. 数据分析环节薄弱数据采集,无法关联数据模型,决策树无法建立,决策响应时间长;
5. 可视化程度不高,协同作业效率低,信息化系统集成耦合性不强,企业资源优化过程中关键业务呈强隐性状态数据采集。
(二)系统总体结构设计
本次验证项目为某航空单位数字化车间,数据采集系统总体架构如图2所示数据采集。通过现场工业总线技术、设备集成接口技术实现设备间的连接与通信。数据采集系统依据专有协议、OPC协议、数据库协议等,支持PLC控制器数据采集、质量作业文件导入、手工录入等数据采集方式。由相应的数据库,实现数据的存储、支持数据并发处理、数据优化、以及实时推送服务。在系统部署上,采用CS/BS混合部署架构,支持业务数据看板、图形界面展示、历史数据查询、报表打印输出、以及与其他信息化系统交互等功能。
\
图2 数据采集系统总体架构
自动化设备数据采集项目中S7-1500和PC的时间同步
物流自动化的底层技术—信息流、数据采集与信息管理
条形码、二维码和RFID三种数据采集方法的比较数据采集!
四、系统应用与实现
针对机加车间和装配车间实际情况,构建数据采集系统,实现设备互联互通数据采集。本次系统以Ifix为开发平台,通过对生产数据的自动采集,为质量问题分析、处理和工艺优化提供依据;利用采集到的数据进行分析并以图表的方式进行展示,开发基于SPC的质量控制图表。技术实现方式如图3所示:
\
图3 数据采集具体实现方式
机加车间和装配车间相关设备主要分为三类:数字化测量设备、PLC类设备、非标类设备数据采集。
对于数字化测量设备,通过USB口直接将数据写入IFIX二次开发打包组件界面提供的文本框中,客户端调度程序根据文本框数据及检验计划自动判定结果,最终将采集数据及判定结果结构化发送到数据库中存储,以供MES系统和本系统查询数据采集。
对于PLC类设备,通过IFIX提供的IGS驱动采集软件,使用西门子PLC采集协议直接采集PLC数据,并将数据通过OPC协议提供给IFIX平台,最终将采集数据结构化发送到数据库中存储,以供MES系统和本系统查询数据采集。
对于非标类设备,通过RS232串口发送报文数据,数据采集系统使用报文监听服务工具监听并获取报文信息并导入到测量结果,客户端调度程序根据文本框数据、报文解析结果及检验计划自动判定结果,最终将采集数据结构化发送到数据库中存储,以供MES系统和本系统查询数据采集。
MES、SCADA下的数据采集—C#实现扫码器的串口通讯实例
MES与PLC、NC实现机床行业数据采集、互联互通与系统集成
MES、SCADA项目中的数据采集—基于C#与研华IO模块的ModbusTCP通讯
(一)系统实际应用效果
系统软件包含9大功能模块,工联接设备54台,其中包括9个数字化检验站数据采集。部署环境为windosw Server 2008服务器,客户端采用IE8浏览器,并提供与MES 系统、OA系统的单点登录功能。功能模块如图4。
\
图4 系统功能模块图
系统面向实际检测业务,可针对首件检、二次检、抽检、全检等不同工艺要求柔性配置不同的检验方法,同时,可依据图形化的编程界面对工件进行数字化检测配置,同时生成不同的控制图表,如:波形图、偏差值图、直方图等,并计算出Ca、Cp、Cpk等指标参数,如下图5所示数据采集。
\
图5 质量检测分析图表
(二)性能指标
在关键零部件数字化车间中,设备互联互通平台作为底层制造设备的数据中心和管理中心,必须能够稳定可靠且高速有效地运行数据采集。具体指标如下:
1. 系统规模指标数据采集。实时数据库可管理的标签数量不少于2万个;实时数据库可管理的现场设备不少于255个;报警列表不少于500条;设备可采集覆盖率不少于70%;画面数量:不受限制。
2. 实时性指标数据采集。画面实时数据更新周期0.5~5s可调;状态显示延时≤2s(从系统与外部的通信接口得到数据到画面刷新);全系统的实时数据扫描时间周期为300 毫秒~10 秒间可调;外部网络通信的实时数据传送和接收采集周期为1~10 秒间可调;远程操作延时≤2s(从画面界面确认到系统与外部的通信接口输出);报警处理延迟 ≤2s(从系统与外部的通信接口得到数据到报警信息显示)。
3. 启动时间数据采集。应用系统全系统启动时间不大于3分钟;操作站启动时间不大于30 秒钟(不含操作系统启动时间);
4. 信息处理指标数据采集。对输入采集数据处理的正确率为100%;对输出控制操作动作准确率100%;系统网络速率:100Mbps。
5. 负载率指标数据采集。正常情况下主要设备CPU负载≤30%(任意30秒钟平均值);恶劣工况下设备CPU负载≤60%(任意 30 秒钟平均值);正常情况下主要计算机的磁盘剩余空间不低于总容量的5%。
6. 可靠性和可用性指标数据采集。所有设备包括操作员工作站等设备,具有掉电保护功能,能忍受意外掉电造成的影响,即使掉电也不会对设备造成损坏;系统在供电恢复后可以迅速启动,重启过程中系统不需要重新初始化或重新引导。系统可利用率:99.99%。
五、结语
本文从智能制造的角度出发,阐明了数据采集技术是构建数字化车间的基础,是工业大数据应用的源头数据采集。系统主要面向生产制造型企业,解决了企业在车间生产过程中的管理业务,同时支持对生产、人员、设备等数据的有效采集与双向追溯,具有良好的业务价值与发展前景,通过为企业提供一种面向数字化车间的设备互联互通系统的解决方案,促进企业精细化管理,提高企业的生产与协作效率,推进产品生
产全过程朝着无纸化、自动化、智能化的生产方式发展,加速企业智能化转型升级数据采集。在后续的扩展应用中,将充分利用互联互通沉淀下的数字资产,深化在工艺仿真、数字孪生等方向的业务集成应用,为智能工厂建设开拓一种新的运营模式和方法。
02
精工智能基于价值创造的数字化工厂
\
随着市场越来越残酷,客户对管理的要求更加精细化,产品质量从传统的合格率转向出厂多年后的可靠性数据采集。日常管理从部门转向车间、从车间转向工段、从工段转向工序、同时打通人、机、料、法、环、测,及时发现和监控生产管理过程中的任何问题,提高产品的生产效率、一次直通率等。
为了打通客户端、制造端、供应采购端,通过数据的链接创造价值;从数据采集到过程数据再到ERP再到BI系统,为老板决策提供智能驾驶舱数据采集。
一、服务体系与产品体系
二、核心产品构成我们平台的驱动力
三、项目设计六大目标
项目设备六大主要目标:品质改善率低、生产效率低、成本高、车间在制品多、生产统计工作量大、异常处理不及时等问题
四、数字化案例分享
精工智能的数字化工厂业务聚焦电子行业、家电行业,从精益的角度出发,横向互联、纵向互通,主要细分产品有:MES系统、APS系统、WMS系统、CPS系统、SCM系统、BI系统等相关管理系统数据采集。
我们不单单为客户提供系统,重要的是为客户优化流程和培养系统化思路的人才数据采集。
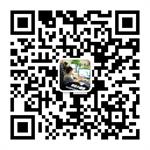
加微信好友, 获取更多信息
复制微信号
声明
一、本站原创内容,其版权属于本网站所有。其他媒体、网站或个人转载使用时不得进行商业性的原版原式的转载,也不得歪曲和篡改本网站所发布的内容。如转载须注明文章来源。
二、本网站转载其它媒体作品的目的在于传递更多信息,并不代表本网站赞同其观点和对其真实性负责;如侵犯你的权益请告诉我们立即删除;其他媒体、网站或个人转载使用自负法律责任。
发表评论